For ten years now, our company has been developing a unique line of expertise in the field of private-laboratory studies on the dynamic behavior of materials, particularly shock physics. This expertise has been built by experienced engineers using some of the most sophisticated experiment tools and numerical equipment in the field. A dedicated workforce, machines and software all combine to uncover the secrets of the physical phenomena associated with shock physics in materials and systems.
The group was not built in a day! Our know-how has been progressively established over ten years. Here are some key dates marking the highlights as we built our expertise in numerical calculation and simulation:
2008: Detonation chamber design.
The expert design work started by ascertaining the mechanisms of interaction between the explosives and the blast containment chambers. Work on developing these chambers, for TNT equivalent masses from several hundred grams to several dozen kilos, all started with defining the “source term”. This involved determining the pressures to which the inner wall of the chamber is subjected when the explosive detonates.
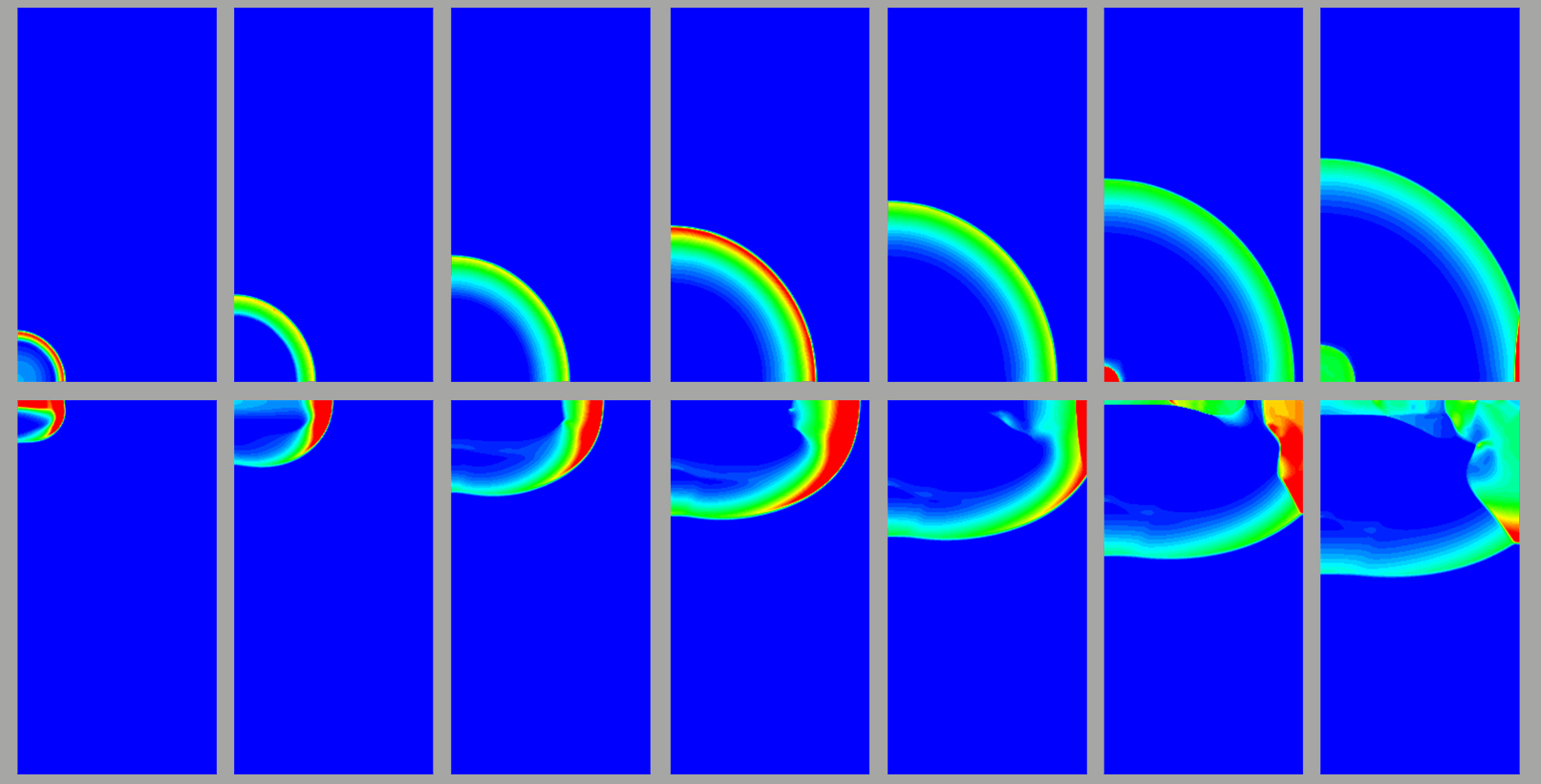
The calculations then involved determining the structure’s response to these initial stress waves and checking that none of the components are stressed beyond its elastic limit. The dialog between the designers and numerical analysts, validating the behavior in response to the shocks, was the key to developing high quality expertise. For these first projects, two engineers were using two software packages and six computing cores.
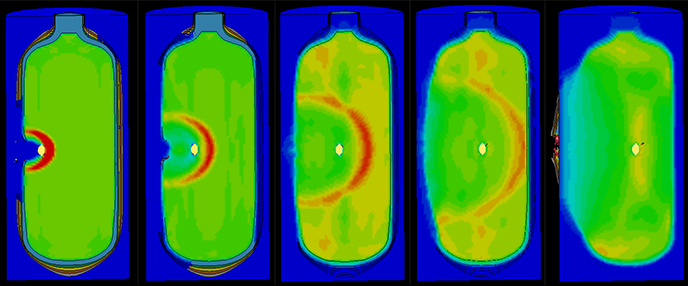
2012: Vulnerability of pressurized tanks.
As part of the CNES (French Space Agency) R&D contract, this study consisted in analyzing the behavior of a satellite reservoir undergoing space debris impacts. A comparison between the tests (performed at 4.5 km/s) and the numerical simulation revealed the main fracture modes for these reservoirs, made of a metal liner with a wound carbon-resin composite outer casing.
The simulations had to combine three equations available in LS-DYNA: Lagrangian, SPH and ALE, with coupling between each of them, which was never done before for this type of simulation. For this study, the number of cores used in the computing rose to 16.
2014: MAUDE and IMPAGREL.
The IMPAGREL and MAUDE programs are two different R&D studies supported by the DGA (French Defense Procurement Agency) and the ANR (French National Research Agency). As part of these studies, we enhanced our expertise by using experiment equipment able to withstand temperature ranges from -100 to +300°C and boosting the simulation equipment to 32 cores.
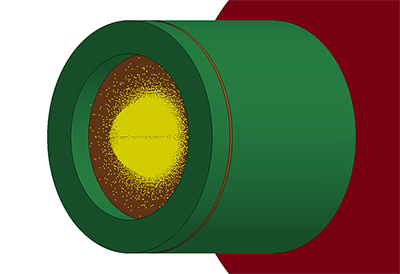
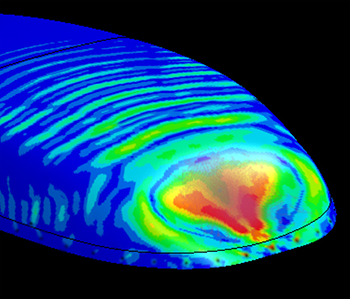
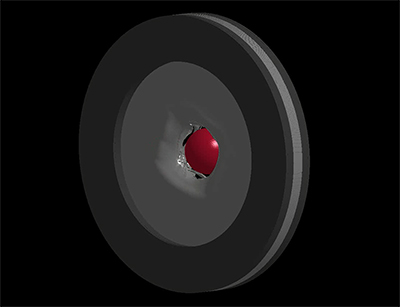
2016: Terminal ballistics.
Several areas of expertise were pooled to study the behavior of aeronautic equipment or components from Light Armored Vehicles (LAVs) when subject to specific stress. For the aeronautics sector, expert studies were carried out on how composite radomes react to bird strikes. The iterative process between the ballistic tests, experiments characterizing the dynamic behavior of the composite materials and numerical simulations led to the rapid certification of this aircraft part.
For the LAVs, the same process resulted in ascertaining the physical phenomena encountered by the various materials when the armor is put through its paces. To complete these studies, six engineers used two software packages and 54 computing cores.
In 2018, our Computing team welcomed an additional engineer and acquired computing equipment with 72 cores. Thiot Ingénierie has therefore kept up with the evolution in numerical technologies, going from a few PCs and a single software license in 2008 to several workstations today, with a potential of 72 parallel cores and three different rapid dynamic software packages. A 100-fold boost to our computing capacity in the space of a decade. In addition, for our specific needs and for our customers, our team is developing software for using our test equipment: the CESAR family for the inner ballistics of launchers, DARTS for CHRONOS and LABHO for Split-Hopkinson bar test analyses.
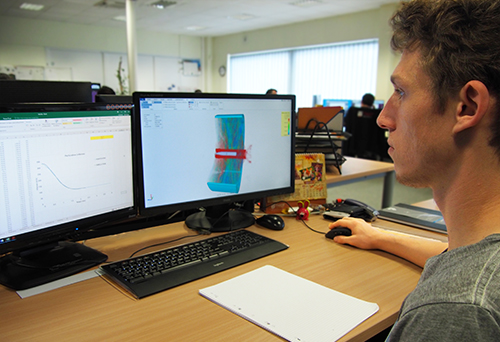
From a human-resources point of view, our Shock Physics group now counts six technicians (operators, draftsmen/designers and metrology specialists) and ten multidisciplinary engineers who work together on a daily basis. Our quality of expertise is down to this constant dialog between the staff carrying out the experiments and the personnel responsible for the numerical simulation, with the different teams sharing their knowledge and know-how. This activity, which is mainly customer-centric, does not however neglect discussions with other players in our field at an international level. Taking part in international conferences and working with major French authoritative bodies (DGA, CNES, etc.) and university laboratories means that our expertise is recognized at the highest levels.