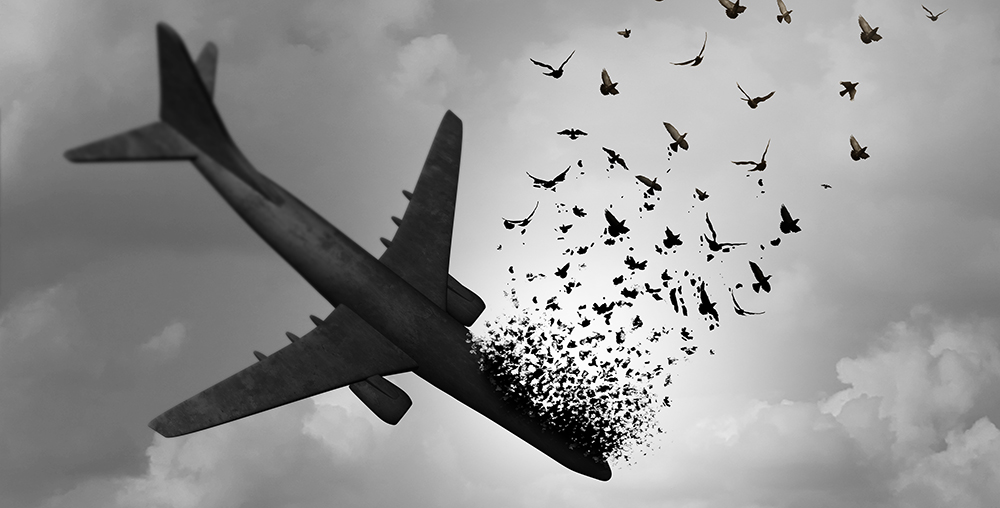
Is a bird no match for a plane? The many incidents recorded each year worldwide arising from a collision between an aircraft and a winged creature seem to show that the opposite is the case. This hazard is commonly known as “bird strike risk”. EASA (European Aviation Safety Agency), the FAA (Federal Aviation Administration, United States) and TC (Transports Canada) have set very comprehensive safety regulatory requirements – including CS-23, CS-25, CS-29, CS-E and CS-P standards for EASA – by monitoring, in particular, the resistance of the structures subjected to bird strikes.
In our shock physics laboratory, we share our expertise with aircraft, engine and equipment manufacturers. We conduct certification tests in short time periods and also perform development tests upstream to assist them in elaborating optimal structures from the design phase of their products. Our strength lies in a combination of tests and numerical simulation to assess the behaviour of all aeronautical structures and allow our customers to quickly obtain their certifications.
Bird strike risk, a real hazard
It is estimated that 35% of the collisions between birds and aircraft give rise to significant damage. In the majority of cases, it is during the take-off or landing phases, while the engines are running at full power, that bird strikes occur. The International Bird Strike Committee reports that 75% of collisions take place at an altitude below 500 feet. Many different species are involved in these collisions including lapwings, seagulls, black-eared kites and barnacle geese but also birds of prey like buzzards, falcons and owls. The infamous US Airways flight 1549 is a perfect example of this. On 15 January 2009, the plane which had just taken off from LaGuardia airport struck a group of Canada geese resulting in a loss of engine power and forcing the captain Chesley Sullenberger to perform an emergency landing in the Hudson River. This spectacular incident was turned into the big-screen release, Sully, directed by Clint Eastwood.
- 1st plane crash recorded in 1912: a seagull crashed into the flight controls and blocked the cables
- 250 deaths caused by collisions between birds and aircraft
- Since 1912, 90 civil aircraft destroyed worldwide
- Between 1950 and 1999, the armies of 32 countries worldwide totalled 286 bird-related air accidents, resulting in the loss of the aircraft or the death of at least one crew member
- The US Air Force records approximately 2,500 collisions per year, and the US civil aviation authority recorded 5,000 collisions in 1999
- The damage costs the United States 650 million dollars each year
Such collisions can generate significant damage, due to the very high speeds at which the two bodies move, ranging from simple deformation of the leading edge of the aircraft wing to the partial or complete destruction of the engine or cockpit canopy. Concerning engines specifically, the suction effect leads to birds being ingested. The result is a collision that can have dramatic consequences, for the bird, certainly, but also for the compressor fins, which can erupt in a domino effect, one after the other, and give rise to a lot of metallic debris. These fragments can, in turn, damage the engine or wings, or pierce the tanks, which can lead to fuel leakage and a risk of ignition. Other risks include mechanical blockages leading to a loss of manoeuvrability of the aircraft.
Risk prevention
Currently, three methods are recommended by the International Civil Aviation Organisation in response to the presence of birds near take-off and landing runways: broadcasting of bird calls, use of cracker shells and, as a last resort, elimination of non-protected bird species. In Spain, falconers patrol daily with their birds of prey to keep hazardous winged creatures at bay.
No agency imposes specific training for pilots regarding bird strike risk. However, flight plans may be prepared according to migratory routes, nature preserves and estuaries where high concentrations of birds can be expected.
Today, aircraft and engine manufacturers must take bird strike risk into consideration when developing and improving their products. For example, while it is not possible to reliably guarantee that an engine will be able to continue working after a bird strike, it is at least possible to shut off the engine and prevent a fire from starting.
Our certification tests
At THIOT INGENIERIE, we correlate physical tests and numerical simulation for several reasons: gelatin strike tests, equipped with state-of-the-art instruments (HV, ultra high-speed cameras, force sensors, speed-measuring systems, strain and acceleration gauges) allow us to firstly collect tangible and reliable data. By integrating this solid base into our calculation tools, we can then simulate impact phenomena on aircraft structures (nose cones, wings, engines, helicopter blades, fuselage, windshields, etc.) from the simplest to the most complex. This combined expertise allows us to accompany our customers to help them optimise the properties of their structures from the development phase and thereby obtain their certifications faster.
What is HV?
These initials stand for heterodyne velocimeter, a super displacement probe or a super speed radar. This measuring method, which uses laser-Doppler interferometry, in fact covers a range of speeds from a few m/s to a few km/s with a response time of approximately a nanosecond. Measurement uncertainty is approximately 1%, which is why this metrological tool plays an essential role in our shock physics laboratory.
Our test facilities also allow us to conduct certification tests relating to dynamic impacts within short time periods. Our gas guns can reach very high impact speeds and are capable of reproducing those of the rotating parts of aircraft (helicopter blades, turbojet engines, etc.) with the possibility of adjusting the temperature of targets.
Our team conducts all types of tests relating to the impact risks that are of concern to the aeronautical industry, whether they be from hail, tires, ice, or stones. Airbus, Airbus Helicopters, Bombardier, Safran and Rolls Royce have already trusted us to participate in the certification of the most advanced aircraft on the market.