The term “plate impact” corresponds to the standard configuration for characterizing the dynamic behavior of materials.
The objectives of the plate impact
It allows to determine:
- the elastic limit (called Hugoniot elastic limit);
- the breaking limit (called spalling limit);
- the points reached under impact which form the Hugoniot curve or dynamic adiabatic of the material
What is a plate impact test?
It consists in projecting a plate called impactor against a fixed plate called target, at an impact speed noted Vp. The impactor is accelerated by means of a laboratory gas gun using a sabot on which the impactor is positioned. This configuration is characterized by a uniaxial deformation regime, as long as the lateral expansion waves do not disturb the uniaxial flow (as illustrated in the figure opposite). After the impact, uniaxial compression waves are generated in the impactor and in the target leading to a uniaxial deformation regime (hatched area). At the periphery of these two elements, relaxation waves generated by the interface with the vacuum disrupt this uniaxial flow by a two-dimensional deformation.
Parameters to be considered to ensure the quality of a plate impact test
The quality depends on two main factors: the vacuum level at the time of impact, and the flatness at impact.
The vacuum before impact must be low enough to avoid a parasitic air cushion between the impactor and the target. Values of 10-3 mbar are reported in the literature, but values of 1 mbar are acceptable provided the volume of the impact chamber is large enough.
The flatness at impact depends on:
- the flatness and parallelism of the impactor and the target used;
- the quality of the bonding between the impactor and the sabot;
- the adjustment of the perpendicularity between the target and the axis of the launcher.
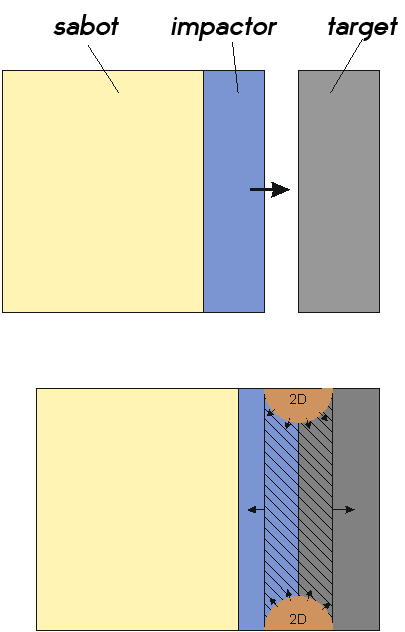
Plate impact test:
Visualization of the uniaxial deformation zone and the two-dimensional deformation zones
The control of these parameters leads to values of 1 mrad as a defect of the flatness at impact.
What measurement methods can be used to make the most of these tests?
Impact tests velocity and impact flatness are measured with timing probes (short-circuit probes, piezoelectric probes) placed around the target with well-defined locations and heights relative to the target plane.
During this test, the quantities measured are the uniaxial stress with electromagnetic gauges or interferometers. These are the ones that are mostly used today because of the accuracy of their measurement compared to other metrological techniques.
As an example, the configuration of an instrumented test with an optical probe connected to a VISAR or VH type interferometer is shown in the figure below. The free surface diagram obtained during this test on a steel type S690QL is shown on the right of this figure.
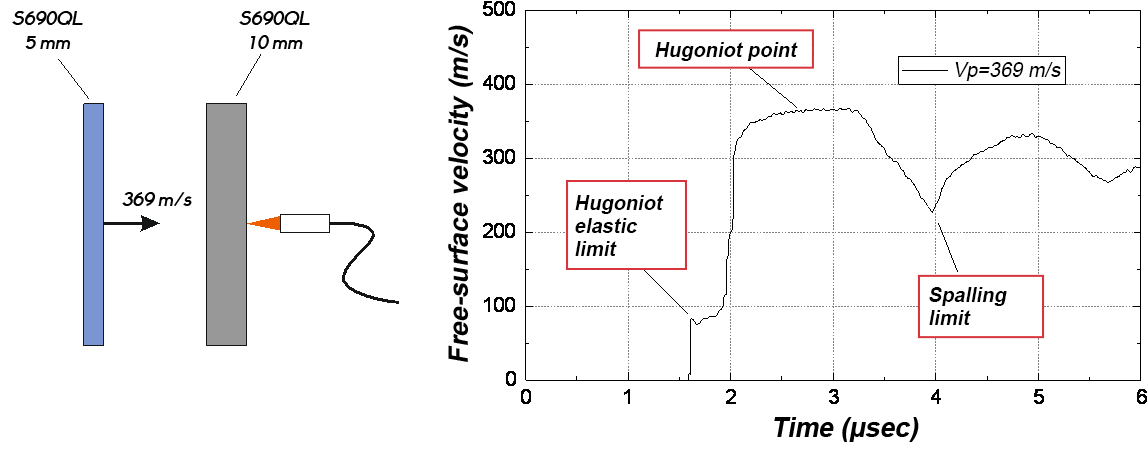
The diagram shows several singularities that correspond to the Hugoniot elastic limit, the spalling limit and the Hugoniot point reached during this test. The stress and strain values are calculated from the velocity values using the conservation of mass and momentum relations expressed for longitudinal wave propagation in uniaxial deformation.
The main advantages compared to other types of dynamic characterization tests
The main advantage of the plate impact test lies in the richness of the configurations it offers. It is thus possible to study the dynamic behavior of the material by a solicitation (compression-relaxation, compression-impact, multiimpact, compression ramp…) by adapting the geometry of the configuration, i.e. by using window materials at the back of the target and impactors composed of several materials of different impedances. To study the behavior of porous materials, for which instrumentation is made difficult by the porosity, we adopt an inverse configuration: the material to be studied constitutes the impactor and the target is a reference material whose behavior under shock is known.
What is the benefit of plate impact testing?
The plate impact test has been used for more than 60 years to characterize the behavior of many materials: metals, polymers, elastomers, ceramics, geomaterials, composites, porous materials and more recently 3D printed materials. This test has contributed to the knowledge of the properties of materials under shock or highly dynamic behavior and in particular to elasto-plastic transitions, viscoelastic and viscoplastic behaviors, porous behaviors, polymorphic transformations and phase changes, damage and failure leading to spalling.